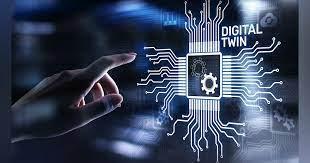
A digital twin is a digital copy of something physical. It is always updated with data from the physical thing. Companies use digital twins to copy their products and manufacturing processes. The digital twins simulate real-world conditions accurately ly. Digital twins let manufacturers see potential issues before they happen. They can also test improvements without disrupting the actual factory. This makes operations smoother and products better.
How Digital Twins Work in Manufacturing?
Digital twins combine data from sensors with computer programs like machine learning. The programs help create detailed digital copies of factory equipment and production steps. These virtual models mirror the physical system in real-time. Manufacturers can experiment safely in the digital environment first. Changes get tested virtually to verify results before applying them in the real factory. Digital twins allow optimizing processes and products without risk or downtime. This flexibility leads to higher quality at lower cost. Digital twins are crucial for modern manufacturing. They give companies an innovative edge in today’s competitive marketplace.
The Role of Digital Twins in Quality Control
Digital twins let you inspect every step of making a product through its virtual model. This lets you spot issues early, before the real product has problems. By finding problems early, you make fewer faulty products. Digital twins help you maintain high quality standards for what you make.
Also, digital twins give you data about your manufacturing in real time. With this data, you can analyze your processes better. You can find areas that are inefficient and improve them. This ongoing cycle of analysis and improvement enhances product quality while reducing waste.
Digital twins give detailed insights, too. You can narrow down exactly where issues occur. Then you can focus your efforts there, optimizing how you use resources. This targeted approach ensures you meet quality standards fully for each product.
Real-time Monitoring and Predictive Analytics
Digital twin tech is great for quality control. It watches the factory floor very closely. It sees everything happening in real time. So, if anything goes wrong, it can spot it right away. And then workers can fix the issue fast. That way, products stay good quality. The digital twin shows exactly what’s happening. So adjustments can be made instantly.
But digital twins do more than just monitor. They predict the future too! Using past and current data, they forecast trends. They warn about potential quality problems before they occur. This gives time for planning. Workers can schedule maintenance or change processes early. That keeps products meeting high standards.
Enhancing Product Design and Customization
Digital twin tech is changing how products get made and customized. It lets designers make very accurate virtual models. With these models, they can test how a product works in many different situations. This helps them find ways to make the product better and customize it for different groups of customers.
First, the digital twin acts as a testing space for new ideas. By putting these virtual models through different environments and uses, designers can spot potential problems early on. They can then fix these issues while still designing the product. This prevents defects later. It also speeds up development, as fewer physical prototypes are needed.
Digital twins also help interact better with customer needs. Changes that would be hard to test on physical prototypes can easily happen in the virtual space. This ensures products meet high standards but also match what customers actually want. So digital twin tech is a must for great product design and customization. It brings new ways to innovate and connect with customers in manufacturing.
Training and Knowledge Transfer
Digital twin technology brings a new way to train employees and share knowledge in manufacturing. It creates a safe, virtual space where workers can learn about the manufacturing process. Through simulations, digital twins let employees explore machinery, see workflows, and practice solving problems without risk. This hands-on learning helps them truly understand.
Digital twins accurately recreate manufacturing steps. They teach workers about product specs, quality rules, and operations. Unlike old training programs, they allow experimentation. Employees make choices and instantly see results, all in a pretend setting. Digital twins do more than just give information. They build a culture of ongoing learning and innovation. Workers better identify quality issues. But they also suggest process improvements. Training this way keeps the workforce up-to-date with new technology. It directly improves product quality and productivity.
Challenges and Considerations
Using digital twin technology in quality control services comes with challenges that manufacturers must understand. One major hurdle is the cost of developing, setting up, and maintaining digital twin systems. Creating detailed virtual models and integrating Internet of Things (IoT) devices and analytics software requires upfront expenses. This can be tough, especially for small and medium businesses. Another key issue is the complexity involved in building and managing these digital copies. Ensuring digital twins accurately represent their physical counterparts demands continuous data synchronization. It also requires processing and analyzing large amounts of information in real-time.
An additional layer of complexity is the strict need for high-quality, real-time data to power predictive analytics and real-time monitoring. This requires robust data collection and management systems, which raises concerns about data security and privacy. Protecting sensitive information from cyber threats is crucial, adding another dimension to the challenge.
Furthermore, the effective use of digital twin technology in quality control depends on having skilled personnel. There is a pressing need for experts who can design, implement, and optimize digital twin systems—a talent pool that is currently limited. Overcoming these hurdles requires strategic planning, ongoing investment in technology and training, and a commitment to navigating the evolving landscape of digital manufacturing technologies.
Conclusion
Blending digital twin tech with 3rd party inspection is a game-changer in manufacturing. It powers up makers to spot issues early, fine-tune methods, and deliver goods that delight customers. Though rolling out digital twins requires cash and smarts, the gains promise to level up the playing field. As we move forward, meshing digital twins with quality control will supercharge manufacturing by injecting intelligence, flexibility, and customer focus into production processes. This fusion’s momentum hints at a future where virtual models are key to quality assurance, setting higher bars for manufacturing excellence.